優(yōu)秀的導(dǎo)熱性能主要取決于性能優(yōu)良的新材料。電子產(chǎn)品的工作溫度對(duì)其效率和壽命有著非常大的影響。隨著電子產(chǎn)品體積的減小、集成化程度的提高,其單位面積的產(chǎn)熱越來(lái)越高,有關(guān)研究表明,電子產(chǎn)品在較高溫度下工作時(shí)其壽命呈指數(shù)縮短。因此,導(dǎo)熱性能優(yōu)良的新材料具有重要的實(shí)際意義和研究?jī)r(jià)值。
理想的導(dǎo)熱材料必須具備高的導(dǎo)熱系數(shù)( Thermal conductivity,TC)、低的熱膨脹系數(shù)(Coefficient of thermal expansion,CTE)、足夠的機(jī)械強(qiáng)度以及低的成本。傳統(tǒng)的導(dǎo)熱材料按照其組成可分為:陶瓷導(dǎo)熱材料(Ceramic thermal conductive material,CTCM)、聚合物導(dǎo)熱材料 ( Polymer thermal conductive material,PTCM) 和金屬導(dǎo)熱材料(metallic thermal conductive material,MTCM)。
CTCM 具有高的致密性、低的熱膨脹系數(shù)和高的機(jī)械強(qiáng)度。常見(jiàn)的 CTCM 主要有 Al2O3、SiC、BeO和 AlN等,其熱學(xué)性能如表 1 和圖 1 所示。盡管 CTCM 熱膨脹系數(shù)低,但是其熱導(dǎo)率也較低,且陶瓷的加工成型難度較大,這限制了 CTCM 的廣泛應(yīng)用。
表 1 常見(jiàn)導(dǎo)熱材料的熱導(dǎo)率和熱膨脹系數(shù)

PTCM 具有好的密封性、低的密度、良好的加工性能和低的生產(chǎn)成本等。最常見(jiàn)的 PTCM 為環(huán)氧樹(shù)脂,其熱學(xué)性能見(jiàn)表 1 和圖 1。PTCM 熱導(dǎo)率低(<2 W/(m·K)),熱膨脹系數(shù)較大,穩(wěn)定性差,因此聚合物導(dǎo)熱材料不能滿足高導(dǎo)熱的需求,一般可應(yīng)用于導(dǎo)熱要求不高的封裝材料。
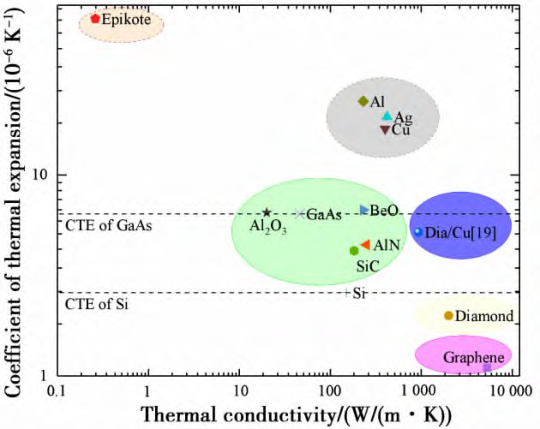
圖 1 常見(jiàn)導(dǎo)熱材料的熱導(dǎo)率和熱膨脹系數(shù)
MTCM 的熱導(dǎo)率一般比聚合物和陶瓷導(dǎo)熱材料的高,這是因?yàn)榇罅康淖杂呻娮哟嬖谟诮饘僦?,可以使熱量的傳遞更迅速。MTCM 易加工、成本低。常見(jiàn)的 MTCM 有銅、鋁、銀等,其熱學(xué)性能見(jiàn)表 1 和圖 1。MTCM 熱導(dǎo)率高,但其熱膨脹系數(shù)與半導(dǎo)體的不匹配限制了其應(yīng)用。
目前單一組分的傳統(tǒng)導(dǎo)熱材料已經(jīng)無(wú)法滿足電子產(chǎn)品對(duì)高熱導(dǎo)率和低熱膨脹系數(shù)的需求,而金屬基復(fù)合導(dǎo)熱材料兼具金屬基體和增強(qiáng)相的優(yōu)點(diǎn),具有高的熱導(dǎo)率、可調(diào)的熱膨脹系數(shù)和良好的力學(xué)性能,因而越來(lái)越受到研究者的關(guān)注。
常見(jiàn)材料的熱導(dǎo)率和熱膨脹系數(shù)見(jiàn)表 1,從表 1 中可知,石墨烯、金剛石等可以作為復(fù)合材料的增強(qiáng)體,銀、銅、鋁等可作為基體。熱導(dǎo)率最高的物質(zhì)為石墨烯,其熱導(dǎo)率最高為 5300 W/(m·K),熱膨脹系數(shù)為 -7×10-6 K-1,其作為增強(qiáng)體有利于提高復(fù)合材料的熱導(dǎo)率,但石墨烯熱學(xué)性能存在嚴(yán)重的各項(xiàng)異性,限制了其作為增強(qiáng)體制備高導(dǎo)熱復(fù)合材料的應(yīng)用。
Huang 等采用真空熱壓燒結(jié)方法制備了石墨片/鋁基復(fù)合材料樣品,該材料在平行于石墨片方向上的熱導(dǎo)率高達(dá) 902 W/(m·K),但其在垂直于石墨片平面方向的熱導(dǎo)率僅為 23.8~73 W/(m·K),且復(fù)合材料在垂直于石墨片方向上的強(qiáng)度極低。金剛石的熱導(dǎo)率最高可達(dá) 2000 W/(m·K),熱膨脹系數(shù)僅為 2×10-6K-1,且性能各向同性,其逐漸成為導(dǎo)熱復(fù)合材料增強(qiáng)體的研究熱點(diǎn)。
Li 等采用溶體浸滲法將 Cu-Zr 合金與金剛石預(yù)制件復(fù)合,制備的復(fù)合材料熱導(dǎo)率可達(dá) 930 W/(m·K),常溫下熱膨脹系數(shù)為 5.2×10-6 K-1,熱物性能十分優(yōu)異。在基體材料的選擇中,兼顧高的熱導(dǎo)率、低的熱膨脹系數(shù)、低的生產(chǎn)成本等因素,銅無(wú)疑是最合適的高熱導(dǎo)率復(fù)合材料的基體。
金剛石/銅復(fù)合材料(Diamond/copper composites,Dia/Cu)綜合了金剛石的超高熱導(dǎo)率和銅基體的低成本、易加工和高熱導(dǎo)率,在高導(dǎo)熱材料應(yīng)用方面具有巨大的潛在價(jià)值,已經(jīng)成為高導(dǎo)熱材料研究的熱點(diǎn)。但是通常金剛石和銅的界面結(jié)合情況較差,即使熔融的銅也很難潤(rùn)濕金剛石,在不施加高壓(≥1GPa) 的條件下,Dia/Cu 界面空隙的存在會(huì)導(dǎo)致其熱導(dǎo)率低于純銅的熱導(dǎo)率,因此界面問(wèn)題已經(jīng)成為高導(dǎo)熱 Dia/Cu 研究的重點(diǎn)。
本文從高導(dǎo)熱金剛石/銅復(fù)合材料的制備和界面調(diào)控兩方面進(jìn)行了總結(jié),并對(duì)金剛石/銅復(fù)合材料未來(lái)的發(fā)展方向進(jìn)行了展望。
金剛石/銅復(fù)合材料的制備技術(shù)
金剛石/銅復(fù)合材料的制備技術(shù)主要包括高溫高壓法(High-temperature high-pressure sintering,HTHP)、真空熱壓燒結(jié)法(Vacuum hot-pressing sintering,VHPS)、放電等離子燒結(jié)法(Spark plasma sintering,SPS)和熔體浸滲法(Infiltration)等。
1.1 高溫高壓燒結(jié)法
高溫高壓法(HTHP)是將混合的粉末填入模具中,在高溫高壓的作用下短時(shí)間內(nèi)制備出復(fù)合材料的方法。在高溫高壓作用下,粉末更易進(jìn)行流動(dòng)傳質(zhì)和擴(kuò)散,燒結(jié)時(shí)間短,制備的材料致密度高。
Pope采用高溫高壓法制備的金剛石/銅復(fù)合材料熱導(dǎo)率高達(dá) 920 W/(m·K),在高溫高壓下金剛石與銅難潤(rùn)濕的情況得到改善,這是由于金剛石二次形核、重結(jié)晶形成了金剛石-金剛石骨架。
在此啟發(fā)下,Yoshida 等在約 1200℃、4.5 GPa 的條件下制備的 Dia/Cu 的熱導(dǎo)率最高為 742 W/(m·K);Ekimov等在8 GPa、1000~1800℃的條件下制備的 Dia/Cu 的熱導(dǎo)率最高為 900 W/(m·K);Chen 等在 1200℃、6 GPa 的條件下燒結(jié) 10 min 得到的燒結(jié)體的最大熱導(dǎo)率為 750 W/(m·K);He等在 1500℃ 、5 GPa 的條件下燒結(jié) 10 min 得到的燒結(jié)體的最大熱導(dǎo)率為 677 W/(m·K)。
高溫高壓法制備的金剛石 /銅復(fù)合材料致密度高,形成的金剛石骨架有助于導(dǎo)熱。但 HTHP 對(duì)模具要求極高,制備的樣品尺寸小、成本高,因此目前還難以被廣泛應(yīng)用。與高溫高壓法相比,真空熱壓燒結(jié)設(shè)備簡(jiǎn)單,模具要求低,燒結(jié)產(chǎn)品尺寸更大。
1.2 真空熱壓燒結(jié)法
真空熱壓燒結(jié)法(VHPS) 是粉末冶金方法的一種,通過(guò)將混合粉末放入模具,在真空熱壓爐內(nèi)經(jīng)歷加熱、加壓、保壓、冷卻、脫模等過(guò)程來(lái)制備復(fù)合材料。真空熱壓燒結(jié)設(shè)備由真空系統(tǒng)、加壓系統(tǒng)和加熱系統(tǒng)三部分組成,設(shè)備示意圖如圖 2 所示。
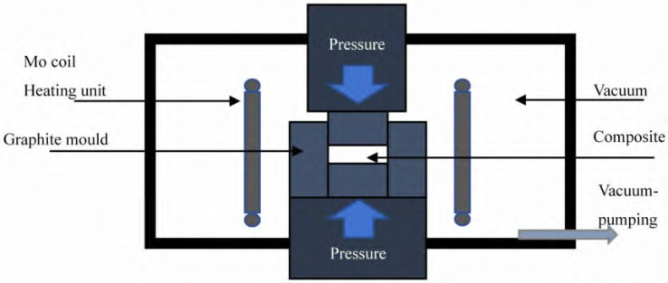
圖 2 真空熱壓燒結(jié)爐示意圖
Shen 等通過(guò)真空熱壓燒結(jié)制備了金剛石/銅合金復(fù)合材料,其相對(duì)密度、熱學(xué)性能隨金剛石體積含量 (0%~20%)的增加而降低。當(dāng)金剛石體積分?jǐn)?shù)為 5% 時(shí),制備的Dia/Cu 熱導(dǎo)率最高為 455 W/(m·K)。
Rape 等增加金剛石的體積分?jǐn)?shù)到 40%,并在銅基體中添加了少量的 Zr,有效改善了 Dia/Cu 界面,復(fù)合材料熱導(dǎo)率可達(dá) 553 W/(m·K)。在此基礎(chǔ)上,Chu 等增加金剛石的體積分?jǐn)?shù)到 55%,研究了 Dia/Cu 界面過(guò)渡層、熱導(dǎo)率等與 Zr 的質(zhì)量分?jǐn)?shù)(0.8%~2.4%)的關(guān)系。結(jié)果表明,當(dāng) Zr 的含量增加時(shí),界面過(guò)渡層逐漸變厚,熱導(dǎo)率呈先提高后降低的趨勢(shì);當(dāng) Zr 的添加量為1.2%時(shí),980℃、40 MPa 下保溫 20 min 制備的 Dia/Cu 的界面厚度約為 320 nm,對(duì)應(yīng)的熱導(dǎo)率最高為 615 W/( m·K)。
Schubert 等研究了真空熱壓燒結(jié)工藝中,在銅基體中引入的不同元素(Zr、B、Al、Ti、Cr)對(duì)復(fù)合材料的影響,結(jié)果表明引入 Cr 和 B 元素制備的 Dia/Cu 的熱導(dǎo)率最高約為 640 W/(m·K)。
而 Zhang 等采用 VHPS 在 900℃、80 MPa 下保溫 30 min 制備了 Dia/Cu,并在金剛石顆粒上設(shè)計(jì)雙層結(jié)構(gòu)(用熱粉末覆蓋燒結(jié)法鍍覆內(nèi)鎢層,再用化學(xué)沉積法鍍覆外銅層),研究了其對(duì) Dia/Cu 結(jié)構(gòu)和性能的影響。結(jié)果表明,在金剛石雙鍍層的作用下,Dia/Cu 熱導(dǎo)率提高到了 721 W/(m·K)。
真空熱壓燒結(jié)具有燒結(jié)過(guò)程中溫度均勻、升降溫速度緩慢、可有效降低復(fù)合材料在燒結(jié)過(guò)程中產(chǎn)生熱應(yīng)力的優(yōu)點(diǎn),而且復(fù)合材料的成分更易控制。但是 VHPS 受模具的限制,其壓力一般在 100 MPa 以下,銅與金剛石界面結(jié)合程度的提升有限,對(duì)燒結(jié)參數(shù)的控制和活性元素的選擇與添加要求較高。VHPS 的制備效率也較低,其制備優(yōu)異熱性能的 Dia/Cu具有一定挑戰(zhàn)。與真空熱壓燒結(jié)法相比、放電等離子燒結(jié)是一種新興、快速、高效的復(fù)合材料制備方法。
1.3 放電等離子燒結(jié)法
放電等離子燒結(jié)法(SPS)是使粉末在脈沖電流和軸向壓力共同作用下通過(guò)瞬間火花放電產(chǎn)生的等離子體進(jìn)行燒結(jié)的方法,其設(shè)備如圖 3 所示。SPS 燒結(jié)時(shí)火花放電點(diǎn)的均勻分布使樣品均勻受熱、快速擴(kuò)散,制備的材料均勻致密,適用于致密化困難的復(fù)合材料的燒結(jié)。
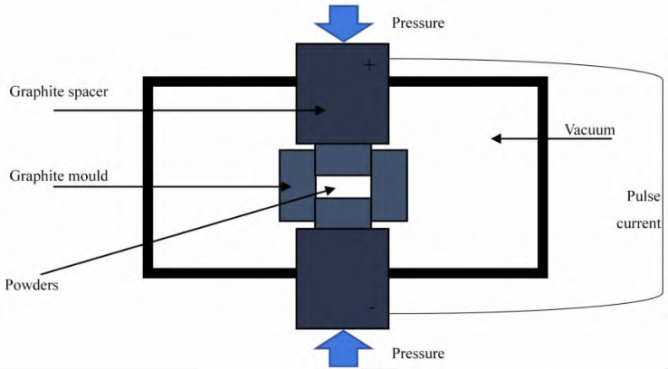
圖 3 放電等離子燒結(jié)示意圖
Zhang 等采用放電等離子燒在 970℃ 、40 MPa 保溫10 min 條件下制備的金剛石/銅復(fù)合材料的熱導(dǎo)率為 493 W/(m·K),復(fù)合材料導(dǎo)熱性能的提高主要是因?yàn)榻饎偸砻娼饘倩纬闪思s 285 nm 厚的均勻 TiC 過(guò)渡層。
Ren等使用真空微蒸鍍?cè)诮饎偸砻驽兏?600~900 nm 厚的Cr 層,并通過(guò) SPS 在 930~950℃ 、37~43 MPa 保溫 15~22 min的條件下制備了 Dia/Cu 復(fù)合材料,其熱導(dǎo)率最高為 657 W/(m·K)。
Schubert 等采用同樣方法制備的 Dia/Cu 的界面處生成了合適厚度的 Cr3C2 層,增強(qiáng)了 Dia/Cu 界面結(jié)合程度,熱導(dǎo)率達(dá)到 640 W/(m·K)。Ciupiński 等使用 SPS 制備的 Dia/Cu 的熱導(dǎo)率可達(dá) 687 W/(m·K),對(duì)應(yīng)的 Cr3C2 過(guò)渡層最佳厚度為 81 nm。
放電等離子燒結(jié)升、降溫快,燒結(jié)溫度相對(duì)低,效率高。通常 Dia/Cu 的燒結(jié)溫度為 800~970℃ ,不會(huì)超過(guò)銅的熔點(diǎn),在該溫度范圍內(nèi)的燒結(jié)模具一般為石墨模具,石墨模具的斷裂強(qiáng)度小于 100 MPa,故燒結(jié)壓力一般為 50~80 MPa,在該燒結(jié)壓力范圍內(nèi)復(fù)合材料很難變得完全致密,材料內(nèi)部的空隙會(huì)增大熱阻,降低 Dia/Cu 的熱導(dǎo)率。因此 SPS 制備金剛石/銅復(fù)合材料的未來(lái)研究方向應(yīng)包括:耐高溫、高強(qiáng)度磨具的開(kāi)發(fā)與選擇,燒結(jié)過(guò)程中界面成分與界面厚度的控制以及研究金剛石/銅復(fù)合材料的熱變形行為,從而提高復(fù)合材料的致密性。
1.4 熔體浸滲法
熔體浸滲法(Infiltration)是將加熱到熔融態(tài)的基體滲透到熔點(diǎn)更高的增強(qiáng)體間隙中,再冷卻、凝固來(lái)制備復(fù)合材料的方法,其中增強(qiáng)體的間隙即是基體的體積分?jǐn)?shù)。熔滲可分為無(wú)壓熔體浸滲法(Pressureless infiltration,PLI) 與壓力熔體浸滲法(Pressure infiltration,PI)。
無(wú)壓熔體浸滲法(PLI)是指熔融態(tài)基體在無(wú)外力的情況下,主要依靠毛細(xì)管力滲透到增強(qiáng)體預(yù)制件的孔隙中制備復(fù)合材料的方法。該法一般采用粘結(jié)劑將金剛石制成預(yù)制件,然后把銅或銅合金置于預(yù)制件之上,在氣體氛圍保護(hù)中升高溫度至銅或銅合金的液相線以上(約 1200℃),銅或銅合金熔體自發(fā)滲透到預(yù)制件中形成金剛石/銅復(fù)合材料。
Dong 等先將表面鍍 Ti 的金剛石與聚乙烯醇混合并壓制成預(yù)制件,再用 PLI 在 1250~1450℃ 高溫下熔滲 30~150 min 得到 Dia/Cu,其相對(duì)密度最高為 99.3%,熱導(dǎo)率最高為 385 W/(m·K)。Chung 等利用 PLI 在 1100℃ 下熔滲 30 min 制備了 Dia/Cu,通過(guò)引入 Ti 使復(fù)合材料熱導(dǎo)率提高到 608 W/(m·K)。
無(wú)壓熔滲條件簡(jiǎn)單,操作方便,最易于實(shí)現(xiàn),但對(duì)基體與增強(qiáng)相之間的潤(rùn)濕性要求高,且在預(yù)制件制備過(guò)程中加入的粘結(jié)劑無(wú)法完全清除,這降低了基體的熱導(dǎo)率,增大了界面熱阻。當(dāng)金剛石體積分?jǐn)?shù)較高時(shí),熔融態(tài)的銅不能自發(fā)地完全填充金剛石的間隙,而壓力熔體浸滲法可以通過(guò)外部壓力促進(jìn)熔體對(duì)空隙的填充。
壓力熔體浸滲法(PI) 是指在滲透過(guò)程中加入外力促進(jìn)滲透并在壓力作用下凝固制備復(fù)合材料的方法。與無(wú)壓熔滲相比,壓力熔滲制備 Dia/Cu 所需時(shí)間短、效率高,制備的Dia/Cu 致密度高,Zhao 等通過(guò) PI 在 1200℃、80 MPa 下熔滲 3 min 制備了 Dia/Cu,發(fā)現(xiàn)金剛石表面鍍 Cr 可以優(yōu)化Dia/Cu 的界面結(jié)合,使復(fù)合材料的致密度提高至 99.6%,抗拉強(qiáng)度提高至 146 MPa。Fan 等用 PI 在 1200℃ 下熔滲3 min制備了 Dia/Cu,研究了銅基體中不同質(zhì)量分?jǐn)?shù)(0.1%~0.5%)的 B 對(duì) Dia/Cu 的熱導(dǎo)率的影響,發(fā)現(xiàn)熱導(dǎo)率與碳化物厚度及分布相關(guān),當(dāng)銅基體中 B 質(zhì)量分?jǐn)?shù)為 0.3%時(shí),Dia/Cu 的熱導(dǎo)率為 711 W/(m·K)。
Wang 等先通過(guò)真空微蒸鍍?cè)诮饎偸砻驽?Cr,再通過(guò) PI 在 1150℃ 下制備復(fù)合材料,其熱導(dǎo)率可提升至 810 W/(m·K)。Li 等通過(guò)同樣的方法在1150℃ 下熔滲 30 min 制備 Dia/Cu,發(fā)現(xiàn)當(dāng) ZrC 過(guò)渡層的厚度約為 400 nm 時(shí),Dia/Cu 的熱導(dǎo)率最高為 930 W/(m·K),熱膨脹系數(shù)為 5.2×10-6 K-1,實(shí)現(xiàn)了高 TC 和低 CTE 的有效結(jié)合。隨后 Li 等研究了 Ti 含量與 Dia/Cu 的熱導(dǎo)率的關(guān)系,發(fā)現(xiàn)過(guò)渡層 TiC 的存在顯著提高了界面的導(dǎo)熱性能,隨著 Ti 含量(質(zhì)量分?jǐn)?shù) 0.3%~2.0%)的增加,Dia/Cu 的熱導(dǎo)率先增后減,當(dāng) Ti 質(zhì)量分?jǐn)?shù)為 0.5%時(shí),熱導(dǎo)率最高可達(dá) 752 W/(m·K)。
壓力浸滲是一個(gè)較為復(fù)雜的過(guò)程,增強(qiáng)體預(yù)制件的制備、基體的熔煉、浸滲過(guò)程中氣體的流動(dòng)以及基體的凝固對(duì)樣品的性能都有很大影響,采用該方法對(duì)石墨模具的設(shè)計(jì)、燒結(jié)參數(shù)的控制和燒結(jié)設(shè)備的選擇要求較高。同時(shí),金剛石在常溫下是碳的亞穩(wěn)態(tài),在高溫環(huán)境下(>900℃) 易發(fā)生石墨化轉(zhuǎn)變。因此,在保證界面結(jié)合的同時(shí),有效降低反應(yīng)溫度是制備具有優(yōu)異綜合性能 Dia/Cu 的關(guān)鍵。
前文介紹的不同制備方法得到的復(fù)合材料的熱導(dǎo)率如圖 4 所示,可以看出高溫高壓法和壓力熔體浸滲法制備的復(fù)合材料熱導(dǎo)率高,這說(shuō)明無(wú)論哪種方法制備的高導(dǎo)熱復(fù)合材料都離不開(kāi)與其相適應(yīng)的壓力。而真空熱壓燒結(jié)和放電等離子燒結(jié)在制備復(fù)合材料中受到模具抗壓強(qiáng)度的限制,使得其熱導(dǎo)率相對(duì)較低,耐高溫、高強(qiáng)度燒結(jié)磨具的開(kāi)發(fā)與選擇將是真空熱壓燒結(jié)和放電等離子燒結(jié)未來(lái)的研究方向之一。以上介紹的各種制備高導(dǎo)熱 Dia/Cu 的技術(shù)都各有優(yōu)缺點(diǎn),研究者需要從實(shí)際出發(fā)選擇合適的制備方法,優(yōu)化工藝,降低成本,改善 Dia/Cu 的界面結(jié)合。
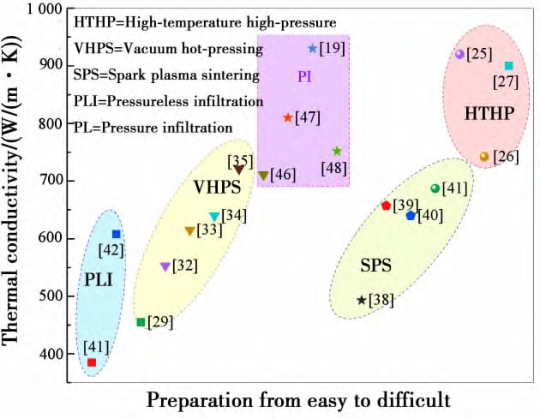
圖 4 不同制備方法制備的復(fù)合材料的熱導(dǎo)率
2.金剛石/銅復(fù)合材料的界面調(diào)控
金剛石與銅之間界面能高、浸潤(rùn)性差的問(wèn)題在降低 Dia/Cu 的力學(xué)性能的同時(shí)還嚴(yán)重降低了其導(dǎo)熱性能。提高Dia/Cu 性能的關(guān)鍵在于優(yōu)化界面結(jié)合、減小界面空隙、減小界面熱阻。目前,除了前文所述的各種燒結(jié)方法外,就是在Dia/Cu 界面處引入與金剛石和銅均有較好結(jié)合能力的過(guò)渡層。通常采用的方法有銅基體合金化(Alloy the copper matrix,ACM) 和金剛石表面金屬化( metallize the diamond surface,MDS)兩類。
2.1 銅基體合金化調(diào)控金剛石/銅界面
銅基體合金化(ACM) 是在銅中摻雜少量活性元素(如Ti、B、Cr、Zr 等)來(lái)改善 Dia/Cu 界面浸潤(rùn)性、優(yōu)化界面結(jié)合。銅基體合金化的主要方法有合金熔煉法 ( Alloy smelting,AS)、氣體霧化法(Gas atomization,GA)等。合金熔煉(AS)是將金屬和添加材料放入加熱爐中熔化,使其發(fā)生物化變化、形成合金的過(guò)程。
Weber 等先通過(guò)AS 制備了 Cu-B、Cu-Cr 合金,再通過(guò)壓力熔體浸滲法制備Dia/Cu,研究發(fā)現(xiàn)當(dāng) B 或 Cr 的含量接近其碳化物形成所需的極限時(shí),Dia/Cu 的熱導(dǎo)率提高,熱膨脹系數(shù)減小。當(dāng) B 的原子分?jǐn)?shù)為 2.5%時(shí),Dia/Cu 的 TC 為 700 W/(m·K),CTE為(6~7)× 10-6 K-1;而當(dāng) Cr 的原子分?jǐn)?shù)為 0.1%時(shí),Dia/Cu的 TC 為 600 W/(m·K),CTE 為 10×10-6 K-1,且 Cr 的加入使得 Dia/Cu 在 1150℃ 時(shí)的潤(rùn)濕角從 130°減小到了 40°,優(yōu)化了界面結(jié)合。
Li 等采用同樣的方法制備了過(guò)渡層為 Zr (Zr 的質(zhì)量分?jǐn)?shù)為 0%~1.0%)的 Dia/Cu,發(fā)現(xiàn)當(dāng) Zr 的質(zhì)量分?jǐn)?shù)為 0.5%時(shí),Dia/Cu 的熱導(dǎo)率最大為 930 W/(m·K),形成的 ZrC 過(guò)渡層均勻完整,最佳厚度約為 400 nm。合金熔煉法簡(jiǎn)單,但通常制備的塊狀銅合金主要用于液相浸滲。氣體霧化法(GA) 是通過(guò)高壓氣流將液態(tài)金屬( 合金)擠壓成液滴,迅速凝結(jié)成粉末的方法,常用于制備銅合金粉末。
Schubert 等先用 GA 制備了 Cu-Cr 合金粉(Cr 的質(zhì)量分?jǐn)?shù)為 8%),再通過(guò) SPS 燒結(jié)制備 Dia/Cu,其 熱 導(dǎo) 率 為640 W /(m·K)。層厚約 100 nm 的 Cr3C2 過(guò)渡層均勻連續(xù),增加了界面結(jié)合,提高了復(fù)合材料的強(qiáng)度和熱學(xué)性能。
Rosinski等使用相同的技術(shù)制備了含 Cr 質(zhì)量分?jǐn)?shù)相同(8%)的 Dia/Cu,過(guò)渡層厚度約為 50~200 nm,結(jié)果表明 Cr 是一種良好的過(guò)渡層材料。Grzonka 等繼續(xù)研究了金剛石不同晶面上 Cr3C2 的形態(tài)、含量和石墨化程度。結(jié)果表明,金剛石表面部分被碳化鉻覆蓋,{111}晶面平均覆蓋率約 43%,{100}晶面平均覆蓋率約 31%,且鉻對(duì)金剛石{100}晶面的石墨轉(zhuǎn)化有強(qiáng)烈的催化作用。GA 可霧化大多數(shù)金屬及合金,工藝成熟,成粉率高,但其噴嘴的結(jié)構(gòu)復(fù)雜,所制得的粉末性能難控。
銅基體合金化引入的合金化元素能夠在金剛石表面形成碳化物過(guò)渡層,改善 Dia/Cu 的潤(rùn)濕性,填充界面間隙,優(yōu)化界面結(jié)合,提高熱學(xué)性能。碳化物層的厚度可通過(guò)活性元素的摻雜量來(lái)控制。但是,添加的各種碳化物形成元素若殘留在基體中,在熱量傳遞時(shí)會(huì)增大聲子散射,降低銅基體的熱導(dǎo)率,進(jìn)而降低 Dia/Cu 的導(dǎo)熱性能。
因此,在選擇摻雜合金元素來(lái)提高熱導(dǎo)率時(shí),要選用易被金剛石碳化且與銅潤(rùn)濕性好的元素,注意避免導(dǎo)熱性能差、在基體中擴(kuò)散嚴(yán)重的元素;同時(shí)要注意把控合金元素的用量,使得碳化物層薄且均勻以減小界面熱阻,避免合金化元素加入量過(guò)少引起的碳化物層不連續(xù)、添加量過(guò)多導(dǎo)致的過(guò)渡層過(guò)厚或者在銅基體中殘留過(guò)多等問(wèn)題。與 ACM 相比,金剛石表面金屬化是在燒結(jié)前預(yù)處理金剛石,可以有效預(yù)防合金元素不足或殘留在銅基體中等所引起的 Dia/Cu 導(dǎo)熱性能降低的問(wèn)題。
2.2 金剛石表面金屬化調(diào)控金剛石/銅界面
金剛石表面金屬化(MDS)是對(duì)金剛石進(jìn)行預(yù)先處理,使金剛石表面與易和碳發(fā)生反應(yīng)的元素(如 Ti、W、Cr、Mo 等)反應(yīng)生成連續(xù)致密的碳化物和活性元素鍍層的過(guò)程。MDS 的方法有化學(xué)鍍法(Electroless plating,EP)、離子濺射法(Ion beam sputtering,IBS)、磁控濺射法(Magnetron sputtering,MS)、真空微蒸鍍法(Vacuum micro evaporation plating,VMEP)、粉末覆蓋燒結(jié)法(Powder covered sintering,PCS)、鹽浴法( Salt bath coating,SBC)和溶膠凝膠法(Sol-gel coating,SGC)等。
化學(xué)鍍(EP)是在無(wú)外電源、有強(qiáng)還原催化劑(Ni、Co 等)作用的情況下,在被鍍表面利用化學(xué)還原反應(yīng)控制金屬沉積的過(guò)程。EP 前,一般要對(duì)金剛石表面進(jìn)行清潔、催化、刻蝕、敏化、活化等預(yù)處理。Niazi 等在金剛石顆粒表面化學(xué)鍍銅,研究了鍍液成分、預(yù)處理?xiàng)l件對(duì)沉積效率、鍍層均勻性、鍍層表面形貌等的影響,得出了最佳的化學(xué)鍍銅工藝?;瘜W(xué)鍍的應(yīng)用不廣泛,主要是因?yàn)?EP 的金屬沉積是物理包裹過(guò)程,導(dǎo)致金剛石與鍍層沒(méi)有實(shí)現(xiàn)冶金結(jié)合;且 EP 過(guò)程中引入的強(qiáng)還原性的催化劑會(huì)促進(jìn)金剛石的石墨化?;瘜W(xué)鍍?cè)贒ia/Cu 中的應(yīng)用還需要進(jìn)一步研究。
離子濺射(IBS)是在真空容器中引入微量的惰性氣體或空氣分子,使其在電場(chǎng)作用下被電離,產(chǎn)生的等離子體轟擊金屬靶材表面,濺射出靶材原子并沉積到金剛石表面的過(guò)程。離子濺射法制備的膜層易附著在金剛石表面,但也特別容易將離子轟擊到膜層中從而影響其性能,利用離子濺射給金剛石表面鍍膜的研究很少。
磁控濺射(MS) 的原理與離子濺射大體相同,但是磁控濺射引入的磁場(chǎng)可以控制陰極靶材附近電子的運(yùn)動(dòng),電離出更多的氣體離子轟擊靶材,提高效率的同時(shí)避免離子轟擊到金剛石表面。
Yang 等采用磁控濺射法在金剛石顆粒上制備了厚度約為 35~130 nm 的光滑致密的 W 鍍層,改善了復(fù)合材料的界面結(jié)合。當(dāng)鍍層厚度為 45 nm 時(shí),采用熔體浸滲法制備的金剛石/鋁復(fù)合材料的熱導(dǎo)率為 622 W/(m·K)。
利用濺射對(duì)金剛石表面進(jìn)行金屬化處理,可精確控制得到的鍍層厚度,但是得到的金剛石顆粒各表面的膜層分布不均勻。為確保鍍層與金剛石的結(jié)合,一般需要在真空(氣氛)爐中處理濺射后的金剛石,使金剛石與鍍層反應(yīng)生成碳化物,反應(yīng)溫度、時(shí)間等都要準(zhǔn)確控制,這增加了表面過(guò)渡層成分和厚度精確控制的難度。
真空微蒸鍍法(VMEP)是在真空容器中,通過(guò)加熱金屬使其氣化逸出的原子與金剛石表面發(fā)生反應(yīng)凝結(jié)生成膜層的過(guò)程。Ren 等先通過(guò) VMEP 控制鍍層成分和厚度,對(duì)金剛石表面鍍覆 Ti、Cr,再用 SPS 制備 Dia/Cu,其熱導(dǎo)率最高為 657 W/( m · K),對(duì)應(yīng)的鍍層最佳厚度為 600~900 nm。
VMEP 工藝簡(jiǎn)單、條件易控,成膜純度高、均勻度好,鍍膜溫度相對(duì)較低,損傷小,成本低,也適用于 W、Ti、Cr、Mo 等碳化物形成元素的鍍覆。但 VMEP 設(shè)備復(fù)雜、維護(hù)費(fèi)用高,且蒸鍍的直射表面鍍覆完整,背面鍍覆卻不充分,在與銅結(jié)合時(shí)會(huì)形成界面缺陷,影響材料的熱物性。
粉末覆蓋燒結(jié)(PCS) 是直接將金屬或金屬化合物與金剛石顆?;旌?,在真空或惰性氣氛高溫爐中使其發(fā)生擴(kuò)散反應(yīng)形成碳化物層的過(guò)程,也稱擴(kuò)散法鍍膜。Bai 等采用PCS 法在金剛石表面鍍覆 B 和 W,研究了預(yù)處理溫度和碳化物形成元素對(duì) Dia/Cu 組織和熱導(dǎo)率的影響,當(dāng)在金剛石表面鍍覆 B 的預(yù)處理溫度為 1040℃ 時(shí),其熱導(dǎo)率可達(dá) 660 W/(m·K)。
Abyzov 等通過(guò) PCS 在 900~1100℃ 下對(duì)金剛石表面進(jìn)行鍍 W 處理,研究了鍍層成分 ( W-W2C-WC)、厚度(5~500 nm)、粗糙度以及雜質(zhì)對(duì)熔滲過(guò)程中潤(rùn)濕性和復(fù)合材料熱導(dǎo)率的影響,結(jié)果表明當(dāng)過(guò)鍍層厚度為110~250 nm 時(shí),Dia/Cu 的熱導(dǎo)率為 900 W/(m·K)。
PCS 法是一種非常實(shí)用的鍍膜方法,條件簡(jiǎn)單,操作方便,鍍覆率高。但是鍍覆時(shí)反應(yīng)溫度高、時(shí)間長(zhǎng),易使金剛石石墨化而損傷金剛石,降低其導(dǎo)熱性能;且鍍覆后金剛石顆粒與金屬粉末難分離。
鹽浴(SBC)是在真空或保護(hù)氣氛的高溫環(huán)境下,金屬粉末和金剛石表面在熔融鹽中反應(yīng)成膜的過(guò)程。Kang 等以MoO3 為反應(yīng)物,通過(guò) SBC 在 900~1100℃ 下反應(yīng) 60 min,在金剛石表面生成了連續(xù)、致密的 Mo2C 膜,研究了 Mo2C 層的形成機(jī)理,再通過(guò)壓力熔滲法制備了 Dia/Cu,其熱導(dǎo)率可達(dá) 596 W/(m·K)。
Kang 等繼續(xù)采用此方法在金剛表面制備了連續(xù)致密的 WC 膜,研究了 WC 過(guò)渡層物相與厚度隨熔鹽溫度的變化規(guī)律,再通過(guò)壓力熔滲法制備了 Dia/Cu,其最大熱導(dǎo)率可達(dá) 658 W/(m·K)。
Molina-Jordá 通過(guò) SBC 在金剛石表面制備了 160 nm 厚的 TiC 膜,再使用壓力熔體浸滲法制備了金剛石/鎂復(fù)合材料,其熱導(dǎo)率最高可達(dá) 716 W/(m·K)。
通過(guò) SBC 制備的鍍層與金剛石的冶金結(jié)合、界面結(jié)合好,且工藝簡(jiǎn)單,效率高,成本低,但 SBC 會(huì)引入熔鹽成分中的雜質(zhì)元素,且 SBC 在高溫下進(jìn)行,金剛石易石墨化。目前,有關(guān)研究表明,KCl-NaCl 的混合鹽體系在 657℃ 即可熔化,可有效避免金剛石的石墨化,保持金剛石的導(dǎo)熱性能,混合鹽體系將使得化學(xué)反應(yīng)更容易實(shí)現(xiàn)。
溶膠凝膠(SGC)是將配置的懸濁液經(jīng)反應(yīng)形成溶膠,然后經(jīng)過(guò)陳化、縮聚形成三維網(wǎng)狀結(jié)構(gòu)凝膠,再加入金剛石混合進(jìn)行鍍層的過(guò)程。
Tan 等使用 SGC 法在金剛石表面鍍 W,再結(jié)合真空熱壓燒結(jié)法和放電等離子燒結(jié)法制備金剛石/鋁復(fù)合材料,研究了納米層的微觀結(jié)構(gòu)及其對(duì)材料熱性能的影響。結(jié)果表明,具有樹(shù)枝狀形貌的 200 nm 厚的 W 納米層改善了金剛石與鋁的界面結(jié)合,提高了界面熱導(dǎo)率,對(duì)應(yīng)的復(fù)合材料熱導(dǎo)率可達(dá)到 599 W/(m·K)。溶膠凝膠法鍍膜,在合適的工藝條件下,所得膜層厚度薄、分布均勻,無(wú)需專門鍍膜設(shè)備,操作簡(jiǎn)單方便,且對(duì)不規(guī)則的金剛石顆粒尤其適宜,但溶膠凝膠的性質(zhì)會(huì)影響成膜的厚度、均勻性,降低材料的導(dǎo)熱性能。
金剛石表面金屬化添加的活性元素在熱處理過(guò)程中易與金剛石表面發(fā)生鍵合反應(yīng),形成的過(guò)渡層與銅具有良好浸潤(rùn)性,同時(shí)還能優(yōu)化界面結(jié)合,提高材料的性能。此外,預(yù)鍍層在制備復(fù)合材料的高溫?zé)Y(jié)過(guò)程中可以保護(hù)金剛石,減少金剛石的損傷,該方法是一種有效、可控的 Dia/Cu 界面優(yōu)化方法。金剛石表面金屬化要選擇易與金剛石表面發(fā)生碳化、與銅潤(rùn)濕性好但不與銅固溶、物質(zhì)本身及其碳化物熱導(dǎo)率相對(duì)較高的元素。
本文介紹的使用不同界面調(diào)控方法制備金剛石/銅的復(fù)合材料的熱導(dǎo)率如圖 5 所示,Dia/Cu 的熱導(dǎo)率與界面調(diào)控的方法和鍍層元素的種類密切相關(guān)。無(wú)論是哪種界面調(diào)控工藝,碳化物形成元素 ( Ti、B、Cr、Zr、W、B、Mo 等) 都有提高Dia/Cu 熱導(dǎo)率的潛力。這些元素與金剛石表面反應(yīng)生成的過(guò)渡層可以改善 Dia/Cu 界面的潤(rùn)濕性和結(jié)合性,提高熱導(dǎo)率。
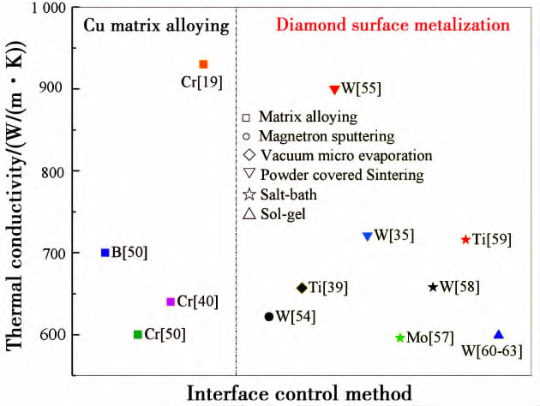
圖 5 不同界面調(diào)控方法制備的復(fù)合材料的熱導(dǎo)率
但是,金剛石/銅復(fù)合材料的實(shí)際熱導(dǎo)率一般都小于理論值,這主要是因?yàn)閷?shí)際生產(chǎn)中 Dia/Cu 的界面結(jié)合未能達(dá)到理想狀態(tài),碳化物的組成、連續(xù)性、厚度等都未實(shí)現(xiàn)精準(zhǔn)控制。
金剛石和銅之間碳化物的物相組成復(fù)雜,鍍層金屬一般為變價(jià)金屬,從金剛石到銅,碳含量逐漸減少,鍍層的物相會(huì)發(fā)生漸變,其熱導(dǎo)率和界面熱阻也會(huì)隨之變化;碳化物層在界面處不連續(xù),會(huì)導(dǎo)致金剛石與銅之間存在空隙,降低復(fù)合材料的熱導(dǎo)率;碳化物層厚度過(guò)薄,界面結(jié)合弱;厚度過(guò)厚,會(huì)產(chǎn)生額外界面熱阻;且碳化物層的存在會(huì)隔斷金剛石-金剛石的高導(dǎo)熱通道,降低復(fù)合材料的熱導(dǎo)率。
研究者應(yīng)結(jié)合實(shí)驗(yàn)條件選擇合適的界面調(diào)控方法展開(kāi)相關(guān)研究,注意分析并解決上述問(wèn)題。
3 結(jié)語(yǔ)與展望
金剛石/銅復(fù)合材料具有高的導(dǎo)熱系數(shù)、與半導(dǎo)體材料相匹配的熱膨脹系數(shù),在軍工、集成電路、5G 通訊和新能源汽車等領(lǐng)域具有廣闊的應(yīng)用前景。國(guó)內(nèi)北京科技大學(xué)、上海交通大學(xué)、天津大學(xué)、北京有色金屬研究總院、中南大學(xué)、哈爾濱工業(yè)大學(xué)、湖南大學(xué)等高校和研究院所相關(guān)課題組對(duì)金剛石/銅復(fù)合材料進(jìn)行了大量的研究,但國(guó)內(nèi)主要是為實(shí)驗(yàn)室或小批量的產(chǎn)品供貨,市場(chǎng)沒(méi)有穩(wěn)定形成,這主要是因?yàn)榕可a(chǎn)需要更加穩(wěn)定的生產(chǎn)工藝。
未來(lái)高導(dǎo)熱金剛石/銅材料的研究應(yīng)重點(diǎn)關(guān)注以下幾個(gè)方面:
(1) 高溫高壓條件下的金剛石-金剛石骨架結(jié)構(gòu)的研究,調(diào)整工藝保證金剛石不被石墨化的同時(shí)金剛石間可以團(tuán)聚成鍵,形成更多高效率的金剛石-金剛石導(dǎo)熱通道,提升復(fù)合材料的導(dǎo)熱性能。
(2) 關(guān)注對(duì)過(guò)鍍層的研究,無(wú)論是哪種制備工藝,過(guò)鍍層對(duì)復(fù)合材料熱導(dǎo)率的提升至關(guān)重要。金剛石與銅之間的過(guò)鍍層要連續(xù)致密、薄且均勻、熱阻小。
(3)從微觀納米尺度對(duì)復(fù)合材料進(jìn)行設(shè)計(jì)-優(yōu)化,揭示納米尺度下各因素(特別是界面結(jié)合)對(duì)復(fù)合材料熱導(dǎo)率的作用機(jī)制及影響規(guī)律。
(4)生產(chǎn)成本同樣重要,目前報(bào)道的金剛石/銅復(fù)合材料的導(dǎo)熱性能已經(jīng)遠(yuǎn)領(lǐng)先于應(yīng)用,其主要原因是成本問(wèn)題。未來(lái),應(yīng)關(guān)注如何使用工業(yè)級(jí)的原料、設(shè)備來(lái)制備高性能導(dǎo)熱材料。
來(lái)源: 材料導(dǎo)報(bào)
原文信息
作者: 郭靖,孟永強(qiáng),孫金峰,張少飛
單位:河北科技大學(xué)材料科學(xué)與工程學(xué)院,河北省柔性功能材料重點(diǎn)實(shí)驗(yàn)室
原文:DOI: 10. 11896/cldb. 20090233