來源 | 電子與封裝
作者 | 杜建宇1,唐睿1,張曉宇2,楊宇馳1,張鐵賓1,呂佩玨1,鄭德印1,楊宇東1,張馳1,姬峰2,余懷強3,張錦文1,王瑋1
單位 | 1. 北京大學(xué)集成電路學(xué)院;2. 北京遙感設(shè)備研究所;3. 中國電子科技集團公司第二十六研究所
原位 | DOI:10.16257/j.cnki.1681-1070.2023.0071
摘要:以 GaN 為代表的新一代半導(dǎo)體材料具有寬禁帶、高電子飽和速率、高擊穿場強等優(yōu)異的電學(xué)性能,使得射頻、電力電子器件有了具備更高功率能力的可能,目前限制器件功率提升的主要瓶頸是缺少與之匹配的散熱手段。具有極高熱導(dǎo)率的金剛石已成為提升器件散熱能力的重要材料,學(xué)術(shù)界針對金剛石與功率器件集成的先進熱管理技術(shù)已經(jīng)開展了大量有益的研究與探索,但是由于金剛石具有極強的化學(xué)惰性和超高的硬度,在實際集成和工藝加工過程中,金剛石-GaN 界面容易出現(xiàn)熱性能和可靠性問題,甚至?xí)?dǎo)致器件失效。對金剛石熱管理技術(shù)的研究進展和存在的問題進行了深入分析,并對未來主要工作方向做了展望。
關(guān)鍵詞:熱管理;功率器件;金剛石;嵌入式冷卻以 GaN 為代表的Ⅲ-Ⅴ族氮化物半導(dǎo)體材料在擊穿電壓、開關(guān)速度等關(guān)鍵電學(xué)參數(shù)上較 Si 材料有著巨大的性能優(yōu)勢,廣泛應(yīng)用于雷達、電子戰(zhàn)系統(tǒng)、蜂巢式基地臺、氣象衛(wèi)星和通信衛(wèi)星等領(lǐng)域,以進一步增強器件的功率密度和提高轉(zhuǎn)換效率。
使用 GaN 材料制備的高電子遷移率晶體管(HEMT)設(shè)備可以提供比現(xiàn)有Si 技術(shù)超 10 倍的功率密度。這種巨大的功率密度會在發(fā)熱結(jié)區(qū)域產(chǎn)生大量的熱,且多以熱點的形式出現(xiàn),這種晶體管級別熱點的局部熱流密度可能超過 10 k W/cm2,若不能將熱量有效地導(dǎo)出至外界,熱量積累造成的高溫會嚴(yán)重影響器件使用壽命、可靠性和性能表現(xiàn),甚至造成芯片的燒毀失效。由于傳統(tǒng)封裝散熱能力較低的限制,目前 GaN 器件只能發(fā)揮其20%~30%的理論性能;隨著功率器件工作溫度的升高,功率器件的失效概率呈指數(shù)級增長。由此可見,傳統(tǒng) GaN 射頻器件封裝帶來的低散熱能力嚴(yán)重影響了射頻器件的電學(xué)性能和工作可靠性。金剛石具有的超高熱導(dǎo)率使其成為了理想的導(dǎo)熱基板,然而,受制于金剛石的超高硬度、高化學(xué)惰性、熱膨脹系數(shù)等性質(zhì),金剛石熱擴散襯底的集成工藝和金剛石微通道加工工藝都具有較大難度。本文總結(jié)了近年來關(guān)于金剛石熱擴散襯底集成與金剛石微通道微納加工技術(shù)的發(fā)展情況,并對未來金剛石散熱襯底的發(fā)展進行了分析和展望。基于高導(dǎo)熱金剛石的熱擴散層及其微納加工技術(shù)傳統(tǒng) GaN 器件的散熱路徑如圖 1(a)所示,熱點位于柵極下方,其熱流會通過 GaN 外延層、氮化鋁(AlN)成核層等多個層間材料擴散至基底中。目前,GaN 基器件多是生長于藍寶石、Si 或 SiC 襯底上,這些襯底的熱導(dǎo)率相對較低,分別為 35 W/(m·K)、150 W/(m·K)、400 W/(m·K),無法滿足器件嚴(yán)苛的熱管理需求,因此需要在芯片熱點近結(jié)區(qū)集成熱導(dǎo)率高的材料來控制器件的溫升。
>
金剛石具有優(yōu)異的絕緣性和超高的熱導(dǎo)率,單晶金剛石在室溫下的導(dǎo)熱系數(shù)高達 2400 W/(m·K),多晶金剛石在室溫下的導(dǎo)熱系數(shù)接近 2000 W/(m·K),是 GaN 基器件的理想襯底材料。所以熱源與金剛石集成后,憑借金剛石的超高熱導(dǎo)率,熱源產(chǎn)生的熱量會迅速地橫向擴散在基板內(nèi),提升了熱源與外界的有效換熱面積,從而可以極大地提升系統(tǒng)的換熱能力。金剛石基 GaN 器件的散熱路徑如圖 1(b)所示。此外,為了進一步加強器件的熱管理性能,也有學(xué)者將嵌入式微流體冷卻技術(shù)的高換熱能力與金剛石的高導(dǎo)熱能力結(jié)合起來。帶微流體的金剛石基 GaN 器件的散熱路徑如圖 1(c)所示,在器件的金剛石襯底上加工微通道,將冷卻工質(zhì)引入至近結(jié)區(qū),以期實現(xiàn)更強的熱管理能力。對于金剛石基 GaN 技術(shù)的研究,按照研究思路大致分為以下 2 種途徑:一是基于沉積生長工藝,在GaN 器件上生長金剛石材質(zhì)或是在金剛石上外延生長 GaN 器件層,以完成熱擴散層的集成;二是基于鍵合工藝,為了降低器件的界面熱阻,在低溫甚至是室溫下,將化學(xué)氣相沉積(CVD)生長的金剛石基板與GaN 器件層進行鍵合。2014 年,美國 Element 公司 (原 Group4 Labs)的BABIC 等開發(fā)了直接在外延生長的 GaN 基片上生長金剛石的工藝。首先在高阻 Si 襯底上生長Al GaN/GaN 的器件層,由于 GaN 上直接生長金剛石通常需要富氫環(huán)境(氫的體積分數(shù)為 95%~99%)和較高的生長溫度(700℃以上),此時 GaN 晶圓受到刻蝕,導(dǎo)致在 GaN-金剛石界面形成空洞和缺陷,進而增加了額外的熱阻。因此,需要一層介質(zhì)來保護 GaN 外延層。隨后晶圓被倒裝安裝在臨時處理片上。之后再去除晶圓下方的 Si 和一些氮化物過渡層,并在暴露的 GaN緩沖層上沉積 50 nm 的介電層,使用熱燈絲化學(xué)氣相沉積(HFCVD)工藝在其上方生長 100 μm 的金剛石,最后從臨時處理片上取下金剛石并去除氮化硅保護層,使用襯底移除的工藝在外延 GaN 上直接生長金剛石的具體流程如圖 2 所示。
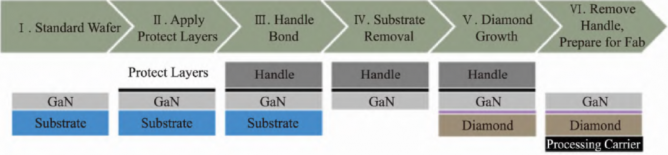
圖2 使用襯底移除工藝在外延 GaN 上直接生長金剛石的流程該方法的關(guān)鍵在于金剛石的生長質(zhì)量,多晶金剛石通常以晶柱的方式生長,在成核的表面迅速形成具有較小尺寸的晶粒。由于聲子在晶界處的散射和吸收,晶核形成過程中的大量晶界無序或錯亂的現(xiàn)象將對導(dǎo)熱性能產(chǎn)生較大的影響。因此,在界面熱阻沒有公認理論模型的情況下,必須通過實驗來測定不同生長工藝生長的金剛石產(chǎn)生的界面熱阻值。2017 年,英國 Bristol 大學(xué)設(shè)備熱成像與可靠性中心(CDTR)的 ZHOU 等比較了 GaN/SiC 直接生長與分別使用 SiN 或 AlN 作為 GaN 和金剛石的阻擋層3 種加工手段產(chǎn)生的界面熱阻,結(jié)果如圖 3 所示。
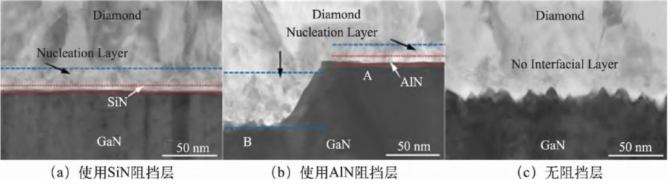
圖3 阻擋層分別為 SiN、AlN 以及無阻擋層的界面熱阻比較以SiC 襯底上 500 nm 厚的 GaN 層為襯底,在 GaN 上生長了 5 nm 厚的非晶態(tài) SiN 或 AlN 阻擋層,在氫氣、氬氣、甲烷(體積分數(shù)為 0.1%~1%)的氣體氛圍中,利用微波等離子體化學(xué)氣相沉積技術(shù)(MPCVD),在微波輸入功率為 2000~2500 W 的工況下,淀積了厚度約為 1 μm 的多晶金剛石層。由于金剛石 /SiN/GaN 樣品產(chǎn)生了粗糙度極低的光滑界面,該金剛石基 GaN 具有已知報道的最低界面熱阻(TBR),約為 6.5 m2·K/GW。2.1.2 金剛石基底生長 GaN 技術(shù)金剛石基 GaN 結(jié)構(gòu)的制備還可以通過在金剛石基底上生長 GaN 來實現(xiàn)。用于加工器件的 GaN 層需要具有足夠高的二維電子氣(2DEG)遷移率和面載流子密度,這要求外延生長的 GaN 層需要具有良好的晶體取向一致性、低的位錯密度、盡可能少且小的表面裂紋以及較低的表面粗糙度。但是 GaN和金剛石的固有材料屬性使外延生長工藝難度較大:①金剛石與 GaN 有較大的晶格失配度(約 13%),這容易導(dǎo)致外延生長的 GaN 具有較大的位錯密度,晶體質(zhì)量不佳;②2 種材料間的熱膨脹系數(shù)(CTE)差別較大,金剛石的 CTE 約為 0.8×10-6 K-1,而 GaN 不同方向的 CTE αa=5.6×10-6 K-1,αc=3.2×10-6 K-1,CTE 失配將產(chǎn)生嚴(yán)重的界面熱應(yīng)力,可能導(dǎo)致 GaN 外延層的開裂、脫落;③當(dāng)外延生長襯底為多晶金剛石時,GaN 與襯底之間沒有固定的晶格外延關(guān)系,外延生長會產(chǎn)生多個不同取向的晶疇,得到連續(xù)的 GaN 晶體會更困難。綜上所述,由于材料的特點,相比在 GaN 基底上生長金剛石,在金剛石基底上生長高質(zhì)量 GaN 需要克服更多的困難,因此近年來的相關(guān)研究較少。早在 2003 年,HAGEMAN 等使用金屬有機物化學(xué)氣相沉積工藝(MOCVD),利用 AlN 作為形核層,在(110)方向的單晶金剛石上沉積初始 GaN 層后,再通過氫化物氣相外延工藝(HVPE)使 GaN 晶粒長大,從而在金剛石上生長了厚度超過 100 μm 的多晶 GaN層。這是最早關(guān)于金剛石上外延生長 GaN 的報道。后續(xù)十幾年,各種在金剛石上外延生長 GaN 的方法被不斷探索,為了避免 GaN 晶體的高度無序,保證 GaN 層的電學(xué)性能,通常需要一個 Si (111)層或 SixN 層作為外延生長的介質(zhì)層,但這種低熱導(dǎo)率的介質(zhì)層也阻礙了熱量的傳遞,并且介質(zhì)層的制備也增加了工藝的復(fù)雜度。2020 年,德克薩斯州立大學(xué)的 AHMED 等使用側(cè)向外延生長工藝(ELO)成功從圖形化的金剛石開口中外延生長出連續(xù)的 GaN 薄膜,實現(xiàn)金剛石基 GaN結(jié)構(gòu),其過程和結(jié)果如圖 4 所示。該課題組首先在 SiN上選擇性地沉積金剛石納米晶粒,使用刻蝕方法使SiN 開口以暴露出 GaN 層,利用該層 GaN 的晶體結(jié)構(gòu),使用 MOCVD 工藝在其上方外延生長成質(zhì)量良好的器件層。

圖4 側(cè)向外延生長制備的金剛石基 GaN 結(jié)構(gòu)金剛石過孔是由美國 Northrop Grumman AS 公司開發(fā)的一種可以改善基底原本散熱性能的方法。由于直接在 SiC 基 GaN 的晶圓上整面生長金剛石會產(chǎn)生熱應(yīng)力問題,高溫下多層材料的熱膨脹系數(shù)不匹配會導(dǎo)致晶圓彎曲甚至破裂,極大地增加了正面光刻和正面器件的處理難度,降低了器件可靠性。于是,研究人員在熱源下方對應(yīng)的 SiC 襯底背面刻蝕深孔,然后通過 MPCVD 技術(shù)將金剛石的顆粒沉積在孔中,圖 5為選擇性生長的金剛石孔 SEM 圖,之后使用基于氧的等離子體刻蝕工藝去除其他區(qū)域的金剛石薄膜,通過這種方式不斷增加孔中的金剛石厚度。該方法可以有效減小金剛石在 GaN 上生長的熱應(yīng)力不匹配問題,減小晶圓的翹曲,使熱點局部微米級范圍內(nèi)的基底熱導(dǎo)率達到 1500 W/(m·K),界面熱阻小于10 m2·K/GW。
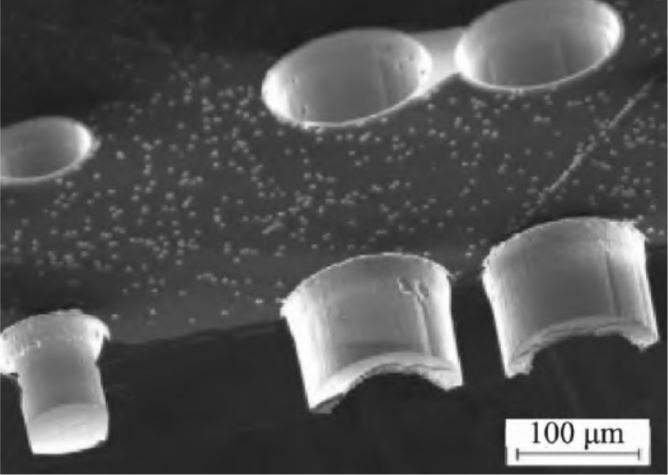
金剛石材料不僅可以作為襯底材料降低 GaN 器件的結(jié)溫,由于其具有優(yōu)良的絕緣特性,多晶金剛石還可以作為散熱鈍化層直接淀積在器件頂部以增強熱點頂部的熱擴散,同樣可以起到增大換熱面積的作用。2012 年,美國海軍研究實驗室(NRL)的 TADJER等成功在 GaN 基 HEMT 頂部制備了高熱導(dǎo)率納米金剛石薄膜(NCD)以取代熱導(dǎo)率較低的 Si3N4鈍化層,器件結(jié)構(gòu)如圖 6(a)所示。這種工藝首先需要使用等離子增強化學(xué)氣相沉積(PECVD)在器件表面制備50 nm 的 SiO2作為 NCD 的阻擋層,之后在 750℃下以 100 nm/h 的速度生長 0.5 μm 的 NCD,圖 6(b)為其SEM 圖。經(jīng)過實測,NCD 散熱鈍化層的散熱性能比SiN 鈍化層更好,使器件的工作溫度下降了 20%。
2019 年,日本富士通公司報道了一種在 GaN 基HEMT 器件表面生長高散熱性能的金剛石薄膜的方法,生長的金剛石在特定晶相上具有微米尺度的晶粒。該團隊在制備好的金剛石散熱鈍化層器件的背面鍵合了高導(dǎo)熱金剛石散熱襯底,制作了金剛石-GaN-金剛石的雙層金剛石散熱結(jié)構(gòu),傳統(tǒng)封裝結(jié)構(gòu)、單層金剛石散熱鈍化層結(jié)構(gòu)與雙層金剛石散熱結(jié)構(gòu)對比如圖 7 所示。經(jīng)過測試,這種雙層金剛石方案具有優(yōu)異的散熱性能,熱點結(jié)溫較傳統(tǒng)封裝下降了 77%。
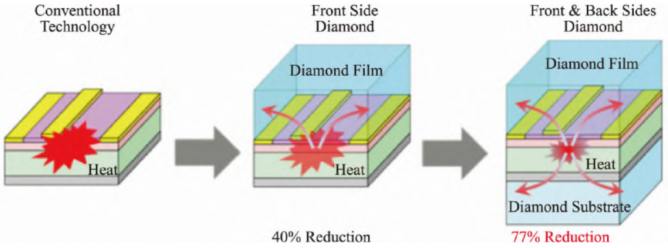
圖7 傳統(tǒng)封裝結(jié)構(gòu)、單層金剛石散熱鈍化層結(jié)構(gòu)與雙層金剛石散熱結(jié)構(gòu)對比盡管實驗結(jié)果已證明使用生長淀積制備金剛石基 GaN 器件的方法可行,但由于生長工藝多是在高溫環(huán)境中進行,容易產(chǎn)生熱應(yīng)力失配等問題,熱應(yīng)力失配會導(dǎo)致器件在材料相交界面處有較大的晶格失配,引起較大的界面熱阻,從而導(dǎo)致金剛石喪失其超高熱導(dǎo)率的優(yōu)勢。且高溫工藝下產(chǎn)生的翹曲會增加器件的后續(xù)工藝加工難度,影響工藝質(zhì)量和生產(chǎn)良率。所以近年來有大量研究聚焦于 GaN 與金剛石基板鍵合集成技術(shù),并為了減小高溫鍵合工藝中熱應(yīng)力的影響,著重開發(fā)了低溫鍵合技術(shù)。1990 年,麻省理工學(xué)院林肯實驗室的 LIAU 等使用了熱鍵合的方法成功鍵合了厘米級大小的Ⅲ-Ⅴ族半導(dǎo)體材料晶圓,并產(chǎn)生了具有正常二極管特性的PN 結(jié),證明了化合物半導(dǎo)體材料鍵合的可行性。之后GaN 在高阻 Si 襯底上的制備工藝日漸成熟,由于 Si襯底易去除的特性,可以獲得質(zhì)量更好的 GaN 晶體用于鍵合。鍵合工藝的優(yōu)勢之一是鍵合前的材料都可以使用最適合的方式進行生長淀積,鍵合材料的質(zhì)量得到了保證,可以最大程度保證金剛石的高熱導(dǎo)率和 GaN材料優(yōu)異的電學(xué)性能,因此鍵合成為了制備金剛石基GaN 器件的重要發(fā)展方向。但是由于金剛石和 GaN 之間熱膨脹系數(shù)的不同,在高溫下鍵合產(chǎn)生的熱失配較大,會導(dǎo)致嚴(yán)重的界面熱阻和可靠性問題,因此近年來許多研究致力于低溫下鍵合工藝的開發(fā)與探索。
2.2.2 低溫鍵合工藝
在美國國防部高級研究計劃局(DARPA)的項目支持下,BAE 的 CHAO 等開發(fā)了一種低溫親水鍵合工藝,其流程如圖 8 所示。
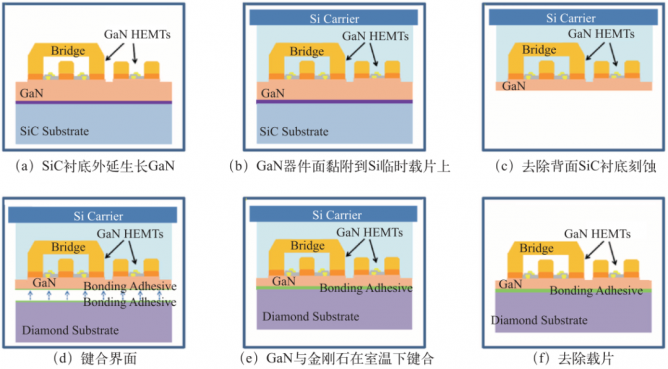
采用 CMP 工藝對裸露出來的鍵合面進行化學(xué)機械拋光,待其均方根表面粗糙度小于 1 nm 后,在金剛石基板和 GaN 的鍵合面上沉積一層薄薄的黏附層,在室溫下使兩側(cè)緊密接觸以進行鍵合。根據(jù)紅外成像和漏電流瞬態(tài)的結(jié)果,金剛石襯底上的 GaN HEMT 器件可以在 10 GHz 工作,最大連續(xù)射頻波(CW)功率密度為 11.0 W/mm,功率附加效率(PAE)為 51%,功率密度比 SiC 基器件行業(yè)標(biāo)準(zhǔn)高3.6 倍。但這種方法制備的金剛石基 GaN 結(jié)構(gòu)的界面熱阻較大,達 34 m2·K/GW,這可能是由低溫親水鍵合導(dǎo)致,鍵合機制容易產(chǎn)生空洞。
2017 年,南京電子設(shè)備研究所的 LIU 等也使用親水鍵合工藝制備了 3 英寸的金剛石基 GaN 器件晶圓,在 180℃下實現(xiàn) GaN 基 HEMT 層與金剛石襯底的鍵合。鍵合后的 GaN 基 HEMT 器件很好地保持了直流和功率性能,最大電流密度為 1005 mA/mm,在10 GHz 時 CW 功率密度達到了 5.5 W/mm ,PAE 為50.5%。發(fā)熱結(jié)到封裝體表面散熱熱阻降低 20%,峰值溫度由 241℃降低到 191℃。
日本學(xué)者 SUGA 等從 20 世紀(jì) 80 年代末開始研究超高真空(UHV)鍵合,在后續(xù) 20 年間取得了長足的進步,該團隊使用表面活化鍵合技術(shù)(SAB)實現(xiàn)了金剛石和 GaN 的室溫鍵合,該方法的顯著優(yōu)勢是避免了在鍵合過程中出現(xiàn)的熱失配和界面空洞,因此理論上可以顯著降低金剛石-GaN 的界面熱阻。然而在SAB 方法中 Ar 離子的轟擊會導(dǎo)致 GaN 表面富含 Ga,金剛石表面則會形成非晶的 C 結(jié)構(gòu),而 C 和 Ga 幾乎不存在化學(xué)作用,難以實現(xiàn) GaN-金剛石的鍵合。使用SAB 方法鍵合不同材料的鍵合強度如圖 9 所示。這為GaN 與金剛石的鍵合帶來了一種新的思路,Si 或其他活性金屬可以成為改善 GaN 與金剛石 SAB 鍵合的介質(zhì)層。
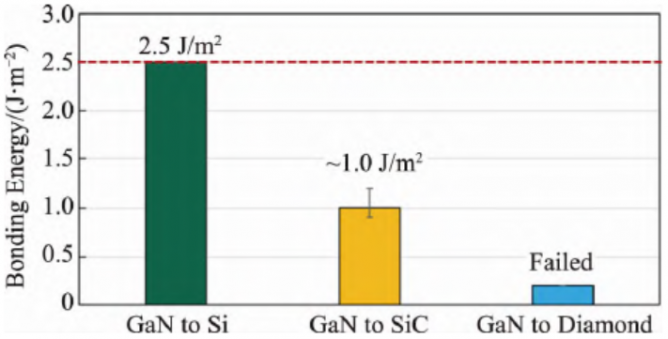
圖9 使用 SAB 方法將 GaN 與 Si、Si C 和金剛石襯底鍵合的強度比較
該團隊后續(xù)用 Si 納米黏附層改善了 SAB 方法,并在含 Si 的 Ar 離子束轟擊下實現(xiàn)了室溫下 GaN-金剛石的直接鍵合。將 2 顆分別使用 CVD 和高溫高壓(HPHT)工藝生長的單晶金剛石鍵合到 GaN 薄膜上,GaN 和金剛石表面的均方根粗糙度分別為 0.4 nm和 0.3 nm。其中,CVD 金剛石利用濺射 Si 的納米黏附層鍵合,采用特殊設(shè)計的離子束源產(chǎn)生的含 Si 的 Ar離子束作用于 HPHT 工藝生長的金剛石來改進 SAB方法。
利用時域熱反射(TDTR)方法測得鍵合界面的界面熱阻分別為 18.9 m2·K/GW 和 10.9 m2·K/GW,明顯高于用傳統(tǒng)高溫方法鍵合的 GaN-金剛石結(jié)構(gòu)。理論分析結(jié)果表明,假定器件的最高工作溫度為 250℃,使用這種方法集成的金剛石基 GaN 器件可以實現(xiàn)的最大功率是 SiC 基 GaN 器件的 2.5 倍,是 Si 基 GaN器件的 5.4 倍。
金剛石的集成對于高功率 HEMT 器件的散熱能力提升十分重要,但是金剛石與 GaN 之間較大的晶格失配使得金剛石較傳統(tǒng)的 Si C 基底來說更難集成。集成質(zhì)量不佳會導(dǎo)致材料分界面處產(chǎn)生較大的界面熱阻,過大的界面熱阻甚至?xí)窒饎偸母邔?dǎo)熱優(yōu)勢,因此如何提高集成質(zhì)量、減小界面熱阻成為了金剛石集成工藝開發(fā)的重要研究方向。GaN-金剛石界面的界面熱阻產(chǎn)生機理如圖 10 所示,主要包括 3 種微觀機制:一是 GaN 和襯底過渡層之間的聲子散射;二是過渡層內(nèi)生成的點缺陷、位錯和其他缺陷導(dǎo)致的聲子散射;三是 GaN 和襯底中近界面的聲子無序散射。
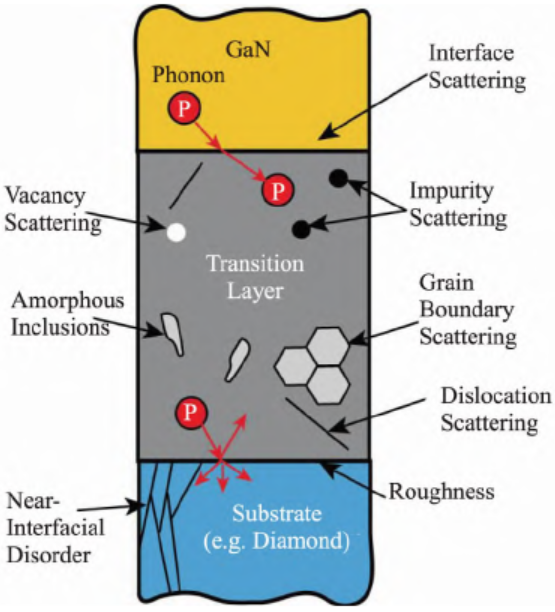
圖10 金剛石與 GaN 器件的界面熱阻產(chǎn)生機理 這3 種機制導(dǎo)致聲子在金剛石-GaN 界面的傳導(dǎo)受阻,宏觀上體現(xiàn)為界面熱阻的上升。有學(xué)者研究了界面熱阻對于 GaN 基器件散熱能力的影響,較大的界面熱阻會導(dǎo)致器件的溫度升高數(shù)十?dāng)z氏度,是導(dǎo)致器件溫升的主要因素之一。
降低金剛石-GaN 界面熱阻是集成方法優(yōu)化迭代的重要方向,近年來由于逐漸開發(fā)的低溫工藝和轉(zhuǎn)移生長工藝,金剛石-GaN 的界面熱阻有了巨大的改善,表 1 展示了近年來文獻報道的金剛石基 GaN 器件的界面熱阻,可以看到,隨著集成工藝手段的不斷提升,界面熱阻得到了巨大的改善。通過表面活化的低溫鍵合、添加納米黏附層等方法所制備的金剛石-GaN 器件有著相對較小的界面熱阻,并可以實現(xiàn)晶圓級別的加工。但是金剛石-GaN 器件的集成機理有待進一步探索,針對界面處的復(fù)雜應(yīng)力問題、微觀失效機理等方面的研究亟需新的發(fā)現(xiàn)和突破。
學(xué)界和業(yè)界已經(jīng)在沉積、鍵合以及界面熱阻優(yōu)化等方面對于 GaN 和金剛石散熱集成熱管理技術(shù)的研究取得了突破性進展,由功率器件產(chǎn)生的熱量可以高效地傳導(dǎo)至金剛石散熱基板內(nèi)并迅速擴散開,但散熱中的另一個問題仍未解決,就是如何將散出的熱量從整個器件中帶走。因此,許多研究團隊想將金剛石基GaN 器件與嵌入式微流體冷卻技術(shù)結(jié)合起來,在集成的金剛石襯底上制備微通道。但金剛石也是自然界中已知最難加工的材料之一,其不僅具有超高的硬度,且?guī)缀鯇λ械幕瘜W(xué)物質(zhì)都有很高的耐性。因此,想在金剛石上制作具有高深寬比、高內(nèi)壁垂直度、復(fù)雜形狀的散熱微通道結(jié)構(gòu)是一項巨大的挑戰(zhàn)。
DARPA 從 2012 年開始啟動芯片內(nèi)/芯片間增強冷卻(ICECool)研究計劃,通過嵌入冷卻液介質(zhì)通道的方式在金剛石基板內(nèi)進行強制對流散熱,從而實現(xiàn)更高的散熱能力,即采用金剛石基 GaN 的嵌入式微流體冷卻技術(shù)將熱量轉(zhuǎn)移到冷卻液中帶走。
在 ICECool項目的資助下,有多家研究團隊開展了該技術(shù)的開發(fā)。國外代表性研究機構(gòu)基于金剛石微通道進行的不同探索如圖 11 所示。
圖11 國外代表性研究機構(gòu)基于金剛石微通道進行的不同探索美國 NGAS 公司采用金剛石過孔與射流冷卻技術(shù)結(jié)合的方法,首先在 SiC 基底的背面選擇性刻蝕過孔,使孔處于熱點的下方,之后在孔內(nèi)沉積金剛石,同時集成了一層 Si 基板射流微通道結(jié)構(gòu),該結(jié)構(gòu)可以使冷卻工質(zhì)直接沖擊金剛石,利用射流滯止區(qū)強大的對流換熱能力有效地將熱量帶走。美國的 Raytheon 公司直接在金剛石基底上刻蝕微通道,并在微通道的下方集成 Si 基的歧管來散熱。美國的 BAE 公司在制備好金剛石基 GaN 器件后,將其貼附在金屬微流道基板上進行器件的冷卻。針對金剛石微流道加工困難的問題,目前有“增材制造”和“減材制造”2 種加工思路,其中增材思路主要是在現(xiàn)有微流道基礎(chǔ)上進行金剛石的沉積,通過覆形的方式加工出微流道,而減材的方式主要是對金剛石基板進行激光燒蝕或反應(yīng)等離子體刻蝕。目前對基于 Si 材料的微流道已有較成熟的研究,并且隨著體硅刻蝕技術(shù)的發(fā)展,硅微流道的深寬比很容易超過 100,具有良好的結(jié)構(gòu)基礎(chǔ)。因此,在現(xiàn)有的硅微流道上沉積金剛石薄層從而制造出金剛石流道成為一種成本低廉、工藝過程相對簡單的金剛石微流道加工方法。以色列理工大學(xué)的 CHANDRAN 等在刻蝕了微通道的 Si 片上使用 HFCVD 技術(shù)沉積了多晶金剛石,成功制備了深度為 45 μm 的金剛石通道,制備的金剛石微通道結(jié)構(gòu)如圖 12 所示。
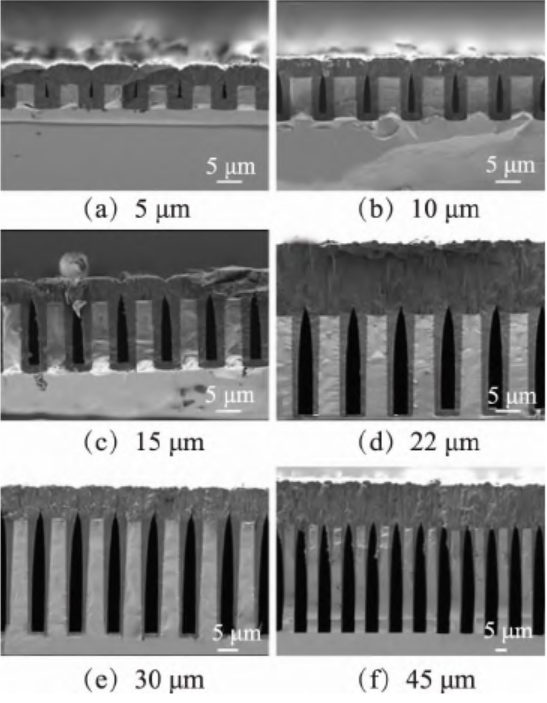
圖12 在 Si 模具上沉積金剛石工藝制備的不同溝槽深度的微通道結(jié)構(gòu)
但該沉積法加工金剛石微流道存在一些顯著的問題:隨著 Si 襯底上流道的深寬比增加,沉積金剛石的氫原子濃度減小,能沉積上的金剛石晶粒深度也逐漸減小,因此這種方法無法支持較大深寬比或較深的金剛石流道制備;同時多晶金剛石因為晶界的存在,雜質(zhì)較多,其導(dǎo)熱特性較單晶金剛石來說較差,導(dǎo)致這種沉積方式加工的金剛石流道散熱性能有所欠缺。
3.2 基于激光燒蝕技術(shù)的金剛石微流道加工方法
在金剛石的材料去除加工類方法中,激光加工已經(jīng)得到了較廣泛的應(yīng)用,在選擇合適的波長、脈沖持續(xù)時間和功率后,該方法可以針對定制材料實現(xiàn)高質(zhì)量的表面和體處理。其原理是通過外部施加能量,使金剛石的 sp3雜化鍵轉(zhuǎn)變?yōu)檩^弱的 sp2雜化鍵,從而去除材料,塑造結(jié)構(gòu)形狀。
2020 年,北京航空航天大學(xué)的 YANG 等采用直流電弧等離子體噴射 CVD 法獲得多晶金剛石薄膜,并將該薄膜加工成 45 mm 長、22.5 mm 寬、3 mm 厚的金剛石襯底,使用飛秒激光燒蝕技術(shù)在金剛石薄膜上制備了 37 個平行三角形微通道,通道長度為 45 mm,水力直徑為 280 μm,每個通道寬度為 300 μm,高度為1500 μm(深寬比為 5)。在高熱流密度(473.9~1000.4 W/cm2)條件下,研究了氨為冷卻介質(zhì)時微通道內(nèi)流動沸騰的換熱特性,散熱器的散熱功率密度達1000.4 W/cm2。2022 年,該團隊將飛秒激光燒蝕方法應(yīng)用于多點熱源的太陽能光伏電池散熱系統(tǒng)中的散熱微流道,在 351.5 W/cm2的熱流密度下,控制熱源表面溫度在 65.9℃以下,且多點熱源之間溫差可以控制在 1.4℃以內(nèi)。飛秒激光燒蝕金剛石微流道掃描電鏡照片如圖 13 所示。
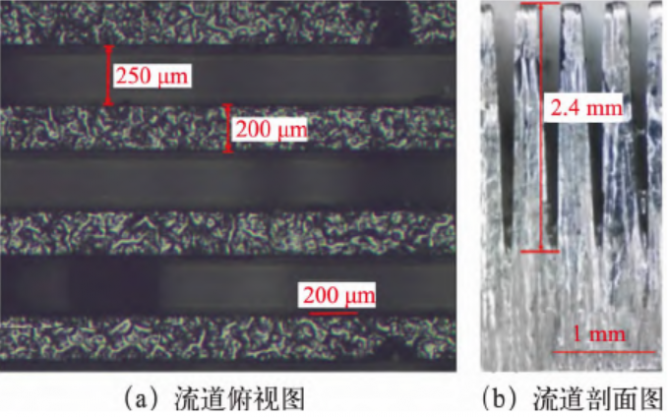
2019 年,西安交通大學(xué)的王宏興教授課題組在HPHT 法制備的金剛石基板上使用水導(dǎo)激光技術(shù)加工出寬度僅為 55 μm 的金剛石溝槽,然后通過 MPCVD工藝讓金剛石流道頂部外延生長厚度約 300 μm 的金剛石,從而形成封閉流道。水導(dǎo)激光加工后外延生長的金剛石微流道如圖 14 所示。
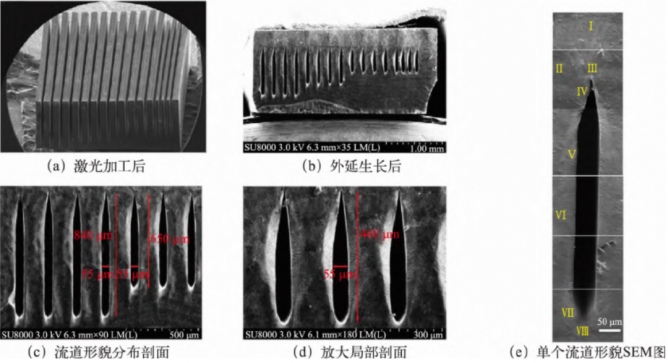
圖14 水導(dǎo)激光加工后外延生長的金剛石微流道該方法制備的金剛石流道深寬比可超過 10,且深度可達 800 μm。該研究利用高于常規(guī)激光加工分辨率的水導(dǎo)激光加工實現(xiàn)了更小寬度的金剛石流道制備,但每條溝槽的加工需要激光掃描 10~20 次,激光束移動速度為 4 mm/s,在進行大尺寸散熱結(jié)構(gòu)批量加工時效率低且成本高。2020 年,北京科技大學(xué)的 QI 等采用 100 k W 直流電弧噴射等離子體化學(xué)氣相沉積(DC Arc Plasma Jet CVD) 系統(tǒng)制備了 4~6 mm 的超厚金剛石膜。以CH4、H2、Ar 為反應(yīng)氣體,在 880℃襯底溫度下開始進行沉積,通過調(diào)控甲烷氣體通量實現(xiàn)晶粒間隙填補、抑制大尺寸柱狀晶異常生長的效果。使用激光在超厚金剛石膜表面加工出 1000 μm 深、330 μm 寬(深寬比為3) 的 V 字形微流道,在熱源熱流密度為 40~120 W/cm2且控制熱源工作溫度為 100℃的情況下,測得對流傳熱系數(shù)為 5637.10~11 447.20 W/ (m2·K),比相同幾何形狀的鋁微流道高 37%~73%。金剛石微流道與商用鋁微流道的結(jié)構(gòu)對比如圖 15 所示。
圖15 金剛石微流道與商用鋁微流道的結(jié)構(gòu)對比3.3 基于刻蝕技術(shù)的金剛石微流道加工方法目前通常采用激光燒蝕來實現(xiàn)金剛石的加工,例如切割金剛石板或金剛石刀具,以及制造微米尺度的透鏡、光柵、微通道等圖形結(jié)構(gòu)。而隨著金剛石生長技術(shù)的進步,高質(zhì)量的金剛石襯底得以商業(yè)化供應(yīng),其中市售的單晶襯底通常規(guī)格可達到幾平方毫米,而多晶襯底則可達到 4 英寸甚至 6 英寸晶圓規(guī)格。加工大尺寸金剛石襯底的需求對加工的速率、并行性、精細度提出了更高的要求,屬于串行加工方法的激光加工逐漸顯露其局限性,而反應(yīng)等離子體刻蝕金剛石的微加工技術(shù)逐漸成為被廣泛研究的課題。刻蝕技術(shù)的優(yōu)點在于綜合利用了光刻的高分辨率、刻蝕加工的并行性以及反應(yīng)等離子體刻蝕后表面的低粗糙度等,該工藝方法目前在金剛石光學(xué)器件微加工領(lǐng)域已有較廣泛的發(fā)展。而金剛石微流道的加工制備對刻蝕深度以及刻蝕深寬比有著較高的要求,在深刻蝕的情況下,負載效應(yīng)導(dǎo)致的刻蝕效率下降也應(yīng)被考慮。2018 年,西安交通大學(xué)的王宏興教授課題組結(jié)合刻蝕工藝與橫向外延生長工藝加工了金剛石微流道。該研究通過磁控濺射的方式在金剛石表面制備了 6 μm 厚的 Al 膜作為刻蝕硬掩模,在 ICP RIE 刻蝕工藝過程中,使用 O2和 Ar 混合的刻蝕氣體配方,成功在金剛石表面加工出凹槽。在此基礎(chǔ)上,通過MPCVD工藝使金剛石橫向外延生長,最終制備得到封閉的金剛石流道。使用 ICP RIE 制備的金剛石微流道溝槽與外延生長后的微流道結(jié)構(gòu)如圖 16 所示。 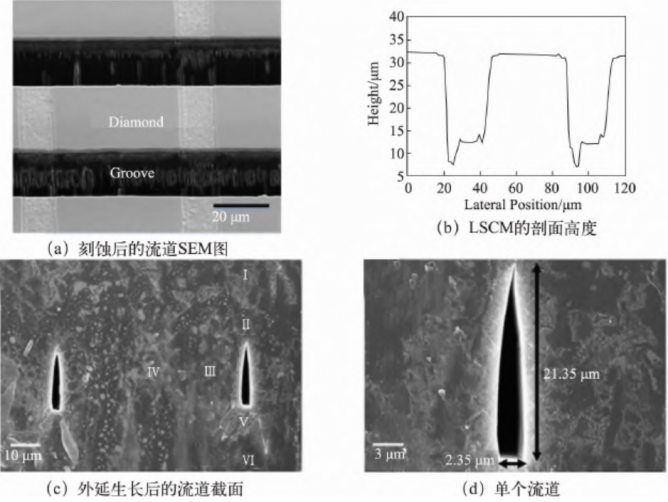
圖16 使用 ICP RIE 制備的金剛石微流道溝槽與外延生長后的微流道結(jié)構(gòu)刻蝕后形成的凹槽結(jié)構(gòu)深寬比約為 1∶1,寬度及深度都約為 20 μm;經(jīng)過橫向外延生長的封閉流道結(jié)構(gòu)深寬比提高到了 10∶1,但流道寬度由于金剛石橫向生長而縮小到約 2 μm,該尺寸對用于散熱的微流道來說過于狹窄,會導(dǎo)致較大的流體壓降。2018 年,悉尼大學(xué)的 TOROS 等僅通過氧等離子 ICP RIE 刻蝕制備的較大深度的金剛石微機械結(jié)構(gòu)如圖 17(a)所示。他們成功制備并釋放了刻蝕深度達150 μm 的微結(jié)構(gòu),且其中槽結(jié)構(gòu)深寬比可達 8∶1,側(cè)壁較平整、垂直,深槽刻蝕測試圖形如圖 17(b)所示,這一研究為金剛石微流道的刻蝕加工提供了思路。
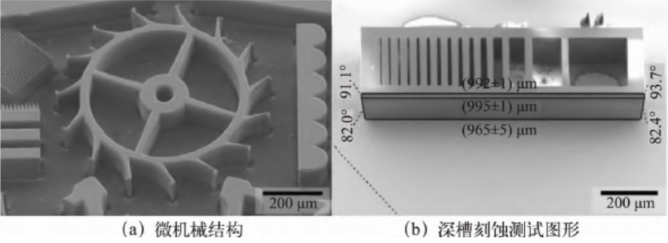
也有學(xué)者將研究聚焦在金剛石刻蝕工藝的控制上,2018 年,美國哈佛大學(xué)的 XIE 等利用氧等離子體對單晶金剛石有晶向選擇性刻蝕的特點,提出了一種通過調(diào)控刻蝕過程中的射頻偏置功率大小從而控制刻蝕暴露出的金剛石晶面的方法。研究結(jié)果表明,不同大小的偏置功率可以準(zhǔn)確對應(yīng)不同的刻蝕面角度,且當(dāng)偏置功率高于 80 W 時,晶向選擇性刻蝕現(xiàn)象基本消失,刻蝕得到的側(cè)壁基本垂直。近年來報道的 ICP RIE 刻蝕金剛石的情況如表 2所示,雖然沒有直接應(yīng)用于散熱微流道加工的研究,但金剛石刻蝕的高速率、高選擇比是各項工作的共同追求,其中也包含對金剛石深刻蝕、精細結(jié)構(gòu)刻蝕的研究,證明了利用刻蝕方式加工微流道具有巨大的潛力。 表2 近年來報道的 ICP RIE 刻蝕金剛石的情況

本文基于金剛石的集成和加工技術(shù),對近年來金剛石材料在高功率器件熱管理中的發(fā)展應(yīng)用情況進行了詳細的綜述。金剛石的高熱導(dǎo)率使其非常適合作為如 GaN 基 HEMT 的高熱流密度器件的散熱基底,解決由于散熱能力不足帶來的性能瓶頸問題,集成金剛石散熱襯底的 HEMT 器件功率性能可以提升數(shù)倍;金剛石微通道熱沉也有效地增強了電子器件的對流換熱能力,顯著地降低了熱阻。然而功率器件與金剛石散熱襯底、金剛石微通道襯底的結(jié)合仍然存在較多問題亟待解決,主要在于以下幾點:一是缺乏對不同方式所形成的功率器件與金剛石襯底之間的界面熱阻深入的理論分析,導(dǎo)致界面熱阻在實際應(yīng)用中難以定量預(yù)測和控制;二是由于金剛石熱膨脹系數(shù)(0.8×10-6 K-1)與常用器件(GaN: αa=5.6×10-6 K-1,αc=3.2×10-6 K-1)的差異較大,在生長、鍵合等集成工藝實施過程中容易產(chǎn)生較大的熱應(yīng)力,器件可靠性無法得到保證;三是由于金剛石的高硬度和高化學(xué)惰性,目前的金剛石微納加工工藝的加工效率相對較低、加工成本高,且難以實現(xiàn)高深寬比、大面積微通道結(jié)構(gòu)的制備,嵌入式液冷技術(shù)的優(yōu)勢無法完全發(fā)揮。綜上所述,應(yīng)用高熱導(dǎo)率金剛石作為熱擴散層甚至微通道基底是進一步提升高功率器件散熱能力的重要手段,具有巨大的研究潛力和應(yīng)用價值,但目前異質(zhì)界面模型、可靠性、高深寬比金剛石加工等理論和工藝技術(shù)問題亟需進一步探索與突破。
(來源:熱管理材料)